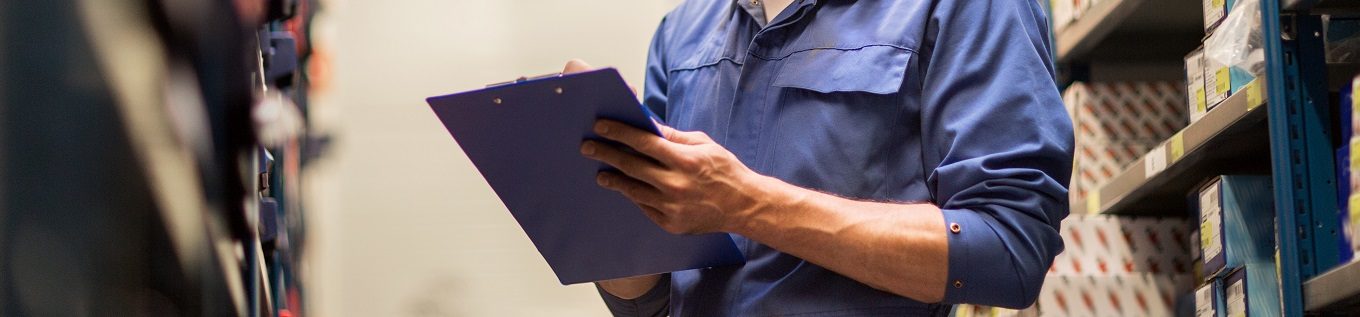
Fully automatic water treatment plants …
….a promise that we gladly make and keep to our customers. You will receive intensive training for the operation of the plant by means of training courses and detailed documentation. Because in order to be able to use the technical and economic advantages in the long run, even the most modern plant technology requires your foresighted maintenance and operation.
Studies show that the plant investment only makes up about 20 % of the total life cycle costs.

BWS therefore relies on a holistic approach that focuses on resource conservation and economic efficiency right from the design stage. In addition, BWS supports you during the plant operation with comprehensive services, so that you and the plant reach your goals permanently.
Together with you, we develop a suitable service concept choosing from many available service modules.
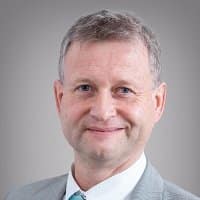
Andreas Widmaier
Head of Service
phone: +49 7423 86880 44
andreas.widmaier@bws-water.com
Your direct line to the BWS-Service:
Some examples of realized service interventions and applications:
DI-water generation for an etching company using a mixed bed cartridge
Installation and commisioning of a mixed bed cartridge for DI-water generation
Technology & plant characteristics:
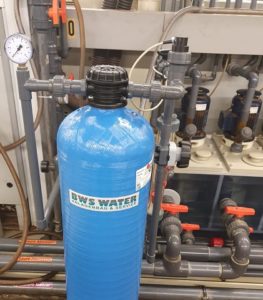
Maintenance of a boiler feed water treatment plant
Complete maintenance and refurbishment of an existing plant for boiler feed water treatment and conditioning in a plastics processing plant.
Completed tasks:
Modernization of a chamber filter press for sludge dewatering in a wastewater treatment plant
Delivery and installation of a new chamber filter press to replace an ageing unit
Completed tasks:

Container plants for cooling tower water conditioning
Delivery of 5 container plants for the conditioning of the cooling tower water of a university institute building
Completed tasks:
Plant optimization with BWS chemicals
Optimization of the waste water treatment of a battery producer by the use of adapted BWS water treatment chemicals
Completed tasks: